Having explored our detailed case studies, that show the real-world impact of our solutions and get inspired on how we can help elevate your project to the next level.
Challenges and Objectives
The client required a comprehensive analysis of their cleanroom to ensure compliance with strict pharmaceutical industry standards. They aimed to evaluate the performance of the cleanroom in maintaining cleanliness, temperature, and humidity levels while accommodating human movement and equipment heat load.
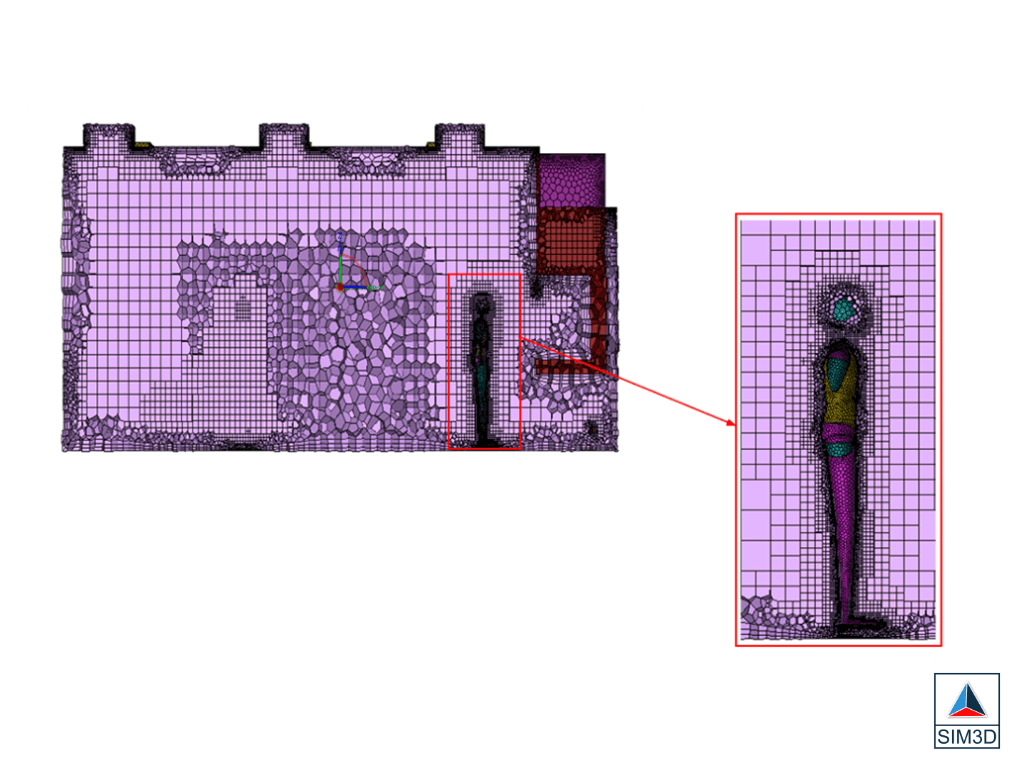
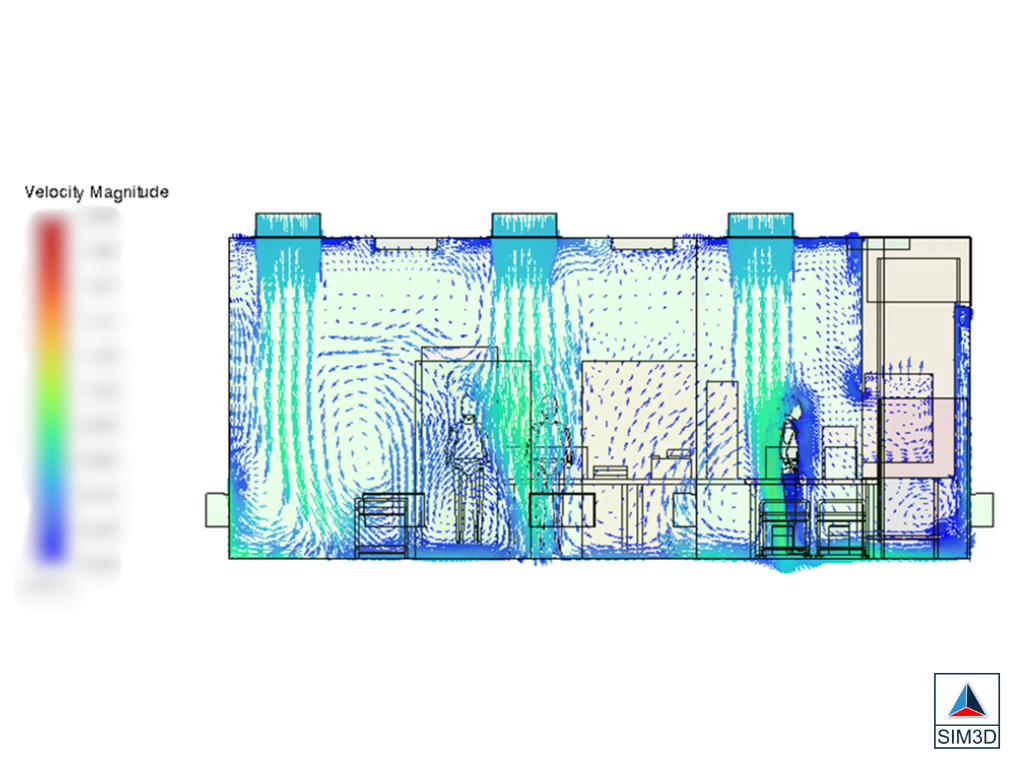
Methodology (Solutions Implemented)
1.Developed a 3D model of the cleanroom.
2.Defined boundary conditions including heat load in equipment, partitions, and walls, as well as inlet and outlet conditions for pressure, velocity, temperature, and relative humidity.
3.Integrated particle generation and tracking details along with human motion parameters.
CFD Analysis:
1.Conducted 3D steady state and dynamic CFD analysis using the defined boundary conditions.
2.Analyzed temperature distribution due to heat dissipation, identified hotspots in the system, and assessed velocity and relative humidity distribution inside the cleanroom.
3.Tracked particles to determine adherence to acceptance criteria.
2.Defined boundary conditions including heat load in equipment, partitions, and walls, as well as inlet and outlet conditions for pressure, velocity, temperature, and relative humidity.
3.Integrated particle generation and tracking details along with human motion parameters.
CFD Analysis:
1.Conducted 3D steady state and dynamic CFD analysis using the defined boundary conditions.
2.Analyzed temperature distribution due to heat dissipation, identified hotspots in the system, and assessed velocity and relative humidity distribution inside the cleanroom.
3.Tracked particles to determine adherence to acceptance criteria.
Benefits (Results Achieved)
1.Successfully identified areas of improvement in the cleanroom\\\\\\\\\\\\\\\’s design and operation.
2.Optimized temperature distribution, ensuring uniformity and reducing hotspots.
3.Improved ventilation efficiency, leading to enhanced air quality and particle control.
4.Enhanced understanding of human motion impact on cleanroom environment.
5.Overall, the analysis contributed to the enhancement of the cleanroom\\\\\\\\\\\\\\\’s performance and compliance with industry standards.
2.Optimized temperature distribution, ensuring uniformity and reducing hotspots.
3.Improved ventilation efficiency, leading to enhanced air quality and particle control.
4.Enhanced understanding of human motion impact on cleanroom environment.
5.Overall, the analysis contributed to the enhancement of the cleanroom\\\\\\\\\\\\\\\’s performance and compliance with industry standards.
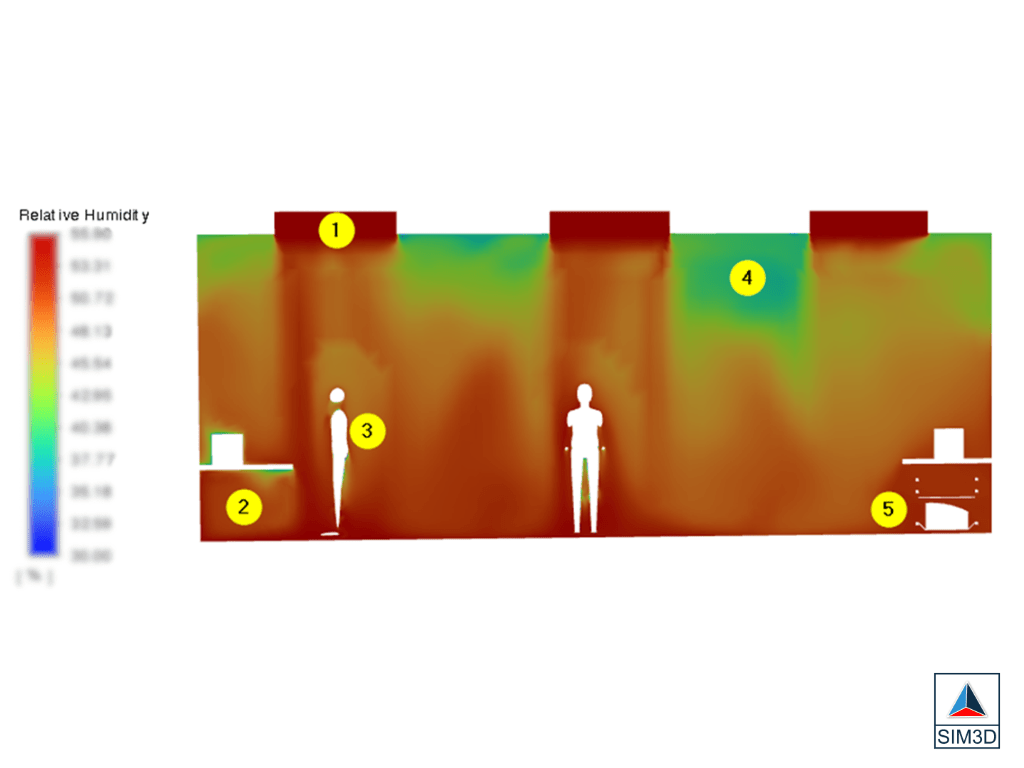
Summary of Project
Through the implementation of 3D steady state and dynamic CFD analysis, the project effectively evaluated and optimized the cleanroom\\\\\\\\\\\\\\\’s performance, leading to improved air quality, temperature distribution, and particle control in the pharmaceutical manufacturing environment. The insights gained from the analysis provided valuable recommendations for enhancing the cleanroom\\\\\\\\\\\\\\\’s design and operation, ultimately ensuring compliance with industry regulations and standards.